By Bob Chabot, Contributing Editor
Squeeze Play
Scan tool manufacturers face a turbulent road ahead.
This article is based on information gethered from presentations given
at this year's SAE OBD II Symposium.
Recent and pending regulatory changes, as well as safety initiatives, in the automobile industry affecting light
duty (LD) and heavy duty (HD) vehicles are creating turbulence for tool manufacturers, especially scan tool makers.
In addition, exponential growth in vehicle complexity, increasing interdependency between systems, a shift in
underlying on-board diagnostics (OBD) architecture and security/safety concerns, coupled with demand from users for
more intuitive ease-of-use and the inclusion of service paths with diagnostics, are putting manufacturers between a
rock and a hard place. These forces will bring challenges to some and opportunities to others. Have you got the
game to survive in these changing times?
User experience matters There seems to be a disconnect between
those who design and manufacture tools and those who use them. Certainly, developers have the priority to ensure
the right functionality, but shouldn’t usability be just as important? Perhaps trying to think like a user or
involving them in product design would result in tools with functionality they want and need. Let me give you two
examples, one from outside the automotive industry and one from within.
Imagine yourself standing third in line at a Starbucks shop waiting to order a cup of plain black coffee. When
asked by the counter serviceperson, Customer One says,” I’d like an iced quad venti non-fat dark cherry mocha.”
Customer Two then orders, “I’ll have an extra-shot, large raspberry large skim mocha on ice.” Does this make you
question whether you – as Customer Three – even knows how to order your drink?
Now, let me ask you a seemingly simple diagnostics question: Can you tell me the exact difference between those
two drinks? Ask a few of your colleagues, and don’t let them write it down. Diagnostics, even in the coffee world,
is exact, I presume. Moreover, it’s a world of service on the fly.
"If you have anything to do with automotive
OBD, attending SAE's OBD Conference in Indianapolis is mandatory," said Bernie Carr of
Bosch Diagnostics. He went on to say, "This event represents the automotive
epicenter for communications and diagnostics. With focus on industry issues and
having automotive experts available for discussion, the forum is easily considered
best in class by offering excellent networking and information gathering
opportunities for ETI members."
|
For the record, the two drinks ordered above are identical, other than one single difference — the flavor. The
worst that can happen should the coffee technician complete a work order incorrectly is that, other than a short
wait, the customer gets an apology and a replacement at no cost. At a price of about $4, most consumers are
unconcerned. But what if, like in the automotive world, that upfront price was $100, or $1,000, or even worse,
unknown? Comebacks then take on a whole new meaning.
Compared to the coffee world, the automotive diagnostics world, its terminology and its technology are just as
industry-specific and mystifying, but the stakes and risk for the customer are ratcheted up. Fear, control,
apprehension, lack of understanding, trust level and other concerns gain a foothold inside a customer’s psyche,
often before even purchasing your tool. The answers lie in how you proactive you are and how you respond to user
concerns: They can be a hurdle or an opportunity to build relationships and a client for life for those who grasp
it.
Now, consider what plays out when a “Check Engine” light comes on: When a tech hooks up a scan tool, the
diagnostic trouble codes (DTCs) are displayed. Of course, we all know it doesn’t end there. A DTC is not a
diagnosis. The on board diagnostic (OBD) system has, however, detected a fault. More diagnosis is almost always
required, often with additional diagnostic tools such as a smoke tester, borescope or multimeter, before any parts
can be replaced. To do otherwise is to play parts roulette and make comebacks a regular occurrence.
With today’s telematics connectivity (e.g. OnStar, Sync, mbrace, AutoLinQ), what if instead of the “Check
Engine” light, a more descriptive and appropriate message popped up on an in-car screen such as “Your vehicle may
have an emissions fault. Your EVAP system circuit has a problem. It’s safe to continue driving your vehicle for a
short period, but your car’s fuel economy, emissions and performance will suffer. You should schedule a service
appointment as soon as possible.” Wouldn’t this make for a more connected motorist-customer?
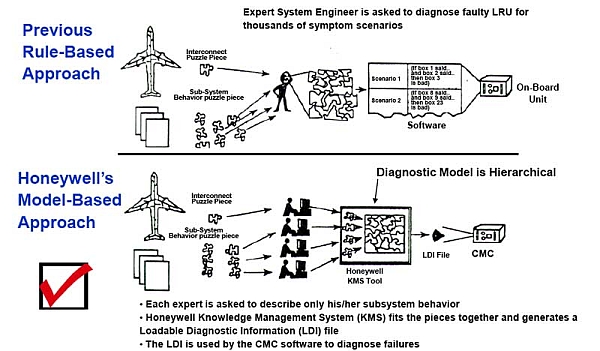
Conditions-Based Maintenance (CBM) is replacing
Rules-Based Maintenance on aircraft. CBM reduces the cost of fault model development and offers
better support for the diagnosis of intermittent faults, prognostic data collection and design
improvement. It also uses limited on-board computing resources and network bandwidth. The next
front may be a migration of CBM to automotive safety-critical electronic systems. (Image — Tim
Felke, Honeywell, presented at 2010 SAE OBD Symposium)
|
Pie in the sky? Recently,
safety has emerged as a growing issue. Safety-related concerns, related legislation under consideration and
innovative passive and active vehicle safety systems (each with OBD) is in the news almost daily. When it comes to
safety, there has been a long history of influence from the aerospace industry upon the automobile industry.
Airplanes have much more complex OBD, prognostic and redundant systems, much of it designed to prevent a
catastrophic fall to earth, says Tim Felke, Engineering Fellow in Honeywell’s Condition-Based Maintenance Group.
The high regard for safety in addition to the higher investment in an airplane relative to an automobile makes the
premium for safety and diagnostics more affordable. Yet technology does transfer to automobiles over time.
Boeing 777s have three multipurpose control display units (CDUs) located on the flight deck that provide data
display and entry capabilities to the pilot for flight management functions. These units are the primary interface
with the integrated Airplane Information Management System (AIMS). Developed in 1991, AIMS replaces the former
system of multiple black boxes and eliminates much of the wiring harness communication on aircrafts. It organizes
everything together in one rack that the OBD modules plug into. This enables higher speed communications between
the modules and allows system partitioning to be optimized around functional blocks, such as power supply modules
and processor modules.
In addition, aerospace conditions-based maintenance OBD architecture employs two supervisory systems. The Crew
Alerting System provides safety-critical indications of loss of function to the flight crew. The Maintenance System
provides nonsafety critical assistance to ground personnel for fault isolation and repair. Line Replaceable Unit
(LRU) modules detect fault conditions and loss of functionality.
“LRUs are responsible for fault containment and recovery,” explains Felke. “Flight deck checklists have been
created for fault conditions that require action by the crew,” He adds that all crew actions are entered into a log
book.
“When something goes awry on a Boeing 777, a schematic of the affected safety system pops on a display in the
cockpit,” says Jack Hendrickson, senior trainer for American Airlines Training and Conference Center in Dallas-Fort
Worth. “The location of where the problem is highlighted on the schematic. The pilot can then touch the screen and
get detailed instructions from the AIMS to address and correct the problem in-flight. If necessary, the pilot can
make arrangements for an emergency landing, if necessary, at the nearest airfield, normally no more than 160 miles
away during a flight.”
While there is typically a time lag before aerospace OBD systems migrate to vehicles, as well as a watering down
of functionality based on need vs. cost, it is unlikely that a pop-up system schematic and OBD remedy system will
show up in vehicles. But given recent safety problems associated with vehicle electronics and the political
attention being paid to them, the potential for more sophisticated OBD safety-related scan tool functionality
appearing in cars is there. For instance, imagine if automotive scan tools diagnosis worked more like a 777’s.
Reining in Diesel “OBD is an unsung hero,” says Tom Cackette,
chief deputy director for the California Air Resources Board (CARB). “California’s goal is to achieve an 80 percent
reduction in CO2-equivalent emissions by 2050. The reality is that if we don’t get started now, we automatically
lose. This means OBD will continue to be an enabler for both LD and HD diesel.”
California Air Resource Board (CARB) emission regulations for HD and LD diesel were formally approved in May
2010, for implementation in 2013. The next planned review is in 2012. For the most part, changes were made to
harmonize HD with LD diesel OBD II regulations, which are newer.
“Diesel engines can be a significant low-emission, high-efficiency powertrain option,” says Joe Kubsch,
executive director of the Manufacturers of Emission Controls Association. “But achieving near-zero exhaust
emissions poses significant future OBD challenges that will drive technological innovation.”
As diesel engines begin to be monitored to the same strict levels as gasoline engines, there will be more and
more need for scan tools to diagnose them. Diesel scan tools will become increasingly more complicated to design
from a software standpoint. These two factors will motivate established LD scan tool manufacturers to enter the
field and cause HD scan tool manufacturers to improve their game.
However some changes regarding HD were made:
- J1962 connector must be mounted to the left of the brake/clutch pedal and it may not be covered by a
door.
- All 2013 and subsequent model-year engines shall have the engine serial number (ESN) available in a
standardized format (e.g. Mode $09, Infotype $0D).
- Only one electronic control unit shall report the ESN to a generic scan tool.
- The addition of Mode $09 IUMPR reporting for diesel fuel system monitor.
- Revised engine idle definition for HD vehicles.
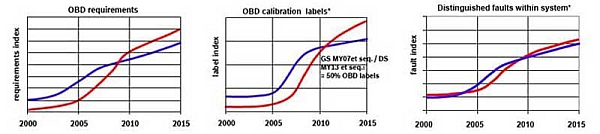
Underlying architecture for scan tools is
headed for change, driven by system type — gasoline (blue) or diesel (red)— and pending applicable
legislation. OBD requirements, the number of OBD calibration labels and number of slots available
for more DTCs and parameter identifiers (PIDs) are rising, especially for diesel. (Image — Gunther
Driedger, Robert Bosch GmbH, presented at 2010 SAE OBD Symposium)
|
Harmony is a moving target Recent attempts to harmonize the
differences in OBD standards and monitoring that exist globally have had limited success. It’s immensely difficult
to braid divergent regulatory systems, each with their own inertia and sense of authorship.
“The worldwide OBD regulatory efforts are not harmonizing in all areas of HD diesel regulation,” notes Jim
Nebergall, a technical advisor with Cummins Inc. “Monitoring requirements are converging in some areas, while
standardization requirements are significantly diverging.”
For example, the United States uses continual malfunction indicator lamp (MIL) behavior as criteria, while
Europe uses discriminatory MIL behavior. Another is the U.S. broader focus on particulate matter, oxides of
nitrogen (NOx), hydrocarbons and carbon monoxide; Europe is only focused on the first two. From a HD certification
standpoint, the United States allows self-certification, while Europe requires witnessed certification.
The gaps that remain impose different requirements on scan tool manufacturers feature sets for different
jurisdictions. “Having common requirements reduces complexity, lowers costs and increases quality and reliability,
with little value to the environment or end-user,” Nebergall adds. Challenges that need to be overcome include
developing a common OBD system that can meet the different sets of requirements and harnessing increased scan tool
development costs.
Shifting architecture Changes to Society of Automotive
Engineers (SAE) or International Organization for Standardization (ISO) documents can mean new or repositioned
connectors, algorithms, coding and scan tool implications. That’s everyday, run-of-the-mill stuff. Major shifts in
underlying network communications architecture are on the near horizon that are poised to impact scan tool
manufacturers.
Relatively slow data transfer speeds and bandwidth limitations are prompting initiatives to move network
communications from controller area network (CAN)-based to other architecture, such as Flexray, Media Orientated
Systems Transfer and ultimately, Ethernet.
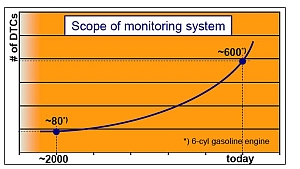
The motivation for the development of FXD as a
new standardized diagnostic exchange format lies in technological progress, evolving complexity of
OBD monitoring systems, the need to be capable of handling more DTCs, and more OBD regulation,
notably for diesel. (Image — Matthias Stampfer, Continental AG, presented at 2010 SAE OBD
Symposium)
|
Another example of architectural change heading downstream is Fault Symptom Exchange Description (FXD), a new
standardized diagnostic exchange format, agreed to by Volkswagen, Audi, Mercedes-Benz, BMW, Porsche, Continental
and Bosch. “The evolving complexity of OBD monitoring systems and regulation has increased the number of DTCs
dramatically,” explains Matthias Stampfer, a spokesperson for Continental AG.
In this joint venture, the automakers defined the requirement, while Continental and Bosch developed the FXD
format, Stampfer adds. The format can accommodate more disparate sources of diagnostic information (photos,
documents, table, mixes) that was driving the generation of consistent and common documentation between OEMs and
suppliers and regulators. FXD is currently being piloted, with the first diagnostic scan tool to be released in
late 2010.
Another architectural concern is security. Carmakers and suppliers are adding smartphone connectivity to
vehicles. Examples include General Motor’s OnStar, Ford’s Sync, and Daimler’s mbrace and Continental’s AutolinQ.
“For the first time, engines can now be started and doors locked by ordinary consumers, from anywhere on the planet
with a cell signal,” states Dave Kleidermacher, chief technology officer at Green Hills Software, which builds
operating system software that goes into vehicles and other embedded systems.
“Manufacturers need to design the systems with security in mind from the very beginning,” Kleidermacher adds.
“You can not retrofit high-level security to a system that wasn't designed for it. People are building this
sophisticated software into cars and not designing security in it from the ground up, and that's a recipe for
disaster.” He notes that there have already been several instances of hacking into electronic systems, including
ones with OBD.
The extension of OBD to monitor and address nonemissions malfunctions to monitor faults is clearly a trend that
scan toolmakers have to address. Examples include airbags, antilock brake system (ABS), electronic stability
program (ESP), active safety systems and app-delivered telematics. In addition, making tools backward-compatible
isn’t always done or possible without driving costs beyond an economic threshold.
It is clear that OBD isn't going away; it’s just going to get more complex and demanding of scan tool
manufacturers. So consider one more trend. Just a few years ago, smartphones and apps didn’t exist. What if scan
tools a few years hence are smartphones or tablets? Would that rock your world?
###
|