By Bob Chabot, Contributing Editor
The Scan Tool Maze
Ensuring that scan
tool purchases advance vehicle
serviceability
The role of scan tools has become both essential and
critical for the complete and safe diagnosis and
repair of modern automobiles. According to John
Jenkins, the founder of CAS of New England,
the independent aftermarket shop has to wrestle with
a number of factors when it comes to scan tool
purchase decisions that will move vehicle
serviceability forward.
According to Jenkins, the scan tool industry’s
marketing vocabulary is a primary source of
confusion for aftermarket facilities making
purchases. He emphasized that to make sound
purchases, buyers need to understand and then
differentiate between four types of scan tools —
OEM, specialty aftermarket, general aftermarket and
OEM-level scan tools. Buyers should be cautious when
they see this last term; it is just a misleading
“marketing” term that does not guarantee that scan
tools labeled or described as such provide the
identical functionality as a factory scan tool.
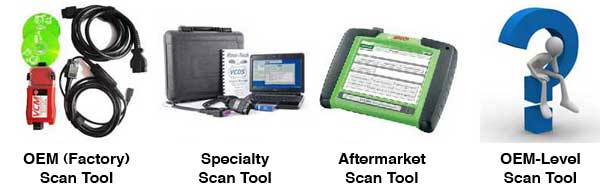
|
Navigating the Scan Tool Maze
"If buyers knew which of four broad
categories their tool alternatives fit
before buying, the functional reality of the
tool would better fit their expectations,"
Jenkins noted. He defined these four scan
tool category as follows:
- OEM (aka factory) scan tools are the
current scan tools used in automakers’
franchised dealer service departments
(e.g. Ford IDS).
- Specialty scan tools focus on
particular car line (e.g. Ross-Tech VCDS
VW/Audi scan tool).
- Multipurpose aftermarket scan tools
are those scan tool built for industry
use that are not a recognized OEM
factory scan tool. (e.g. Bosch KTS 300
or AutoEnginuity OBD 2 scan tools).
- OEM-level scan tools include any
other tool that an aftermarket scan tool
manufacturer wishes to term as such.
This is a “marketing” term that does not
guarantee the factory scan tool
functionality that the term implies.
|
The business focus of Jenkins’ firm is on providing
OEM scan tools, technical support information,
laptops and re-programming to independent automotive
repair shops. He says that equipment and tool
manufacturers should be aware of the key
considerations that can drive service and repair
facilities — their customers — toward original
equipment manufacturer (OEM) scan tools, some that
can sway shops to aftermarket manufacturers’
products, and several emerging trends that are
beginning to shape the scan tool marketplace.
The push toward OEM scan tools
Many technicians in aftermarket shops are frustrated
with aftermarket scan tools. Incomplete coverage, a
lack of functionality necessary for some repairs and
the cost of ongoing updates are just some of the
concerns that push aftermarket facilities towards
OEM (i.e. factory) tooling.
“There are certain efficiencies that can be realized
with OEM tooling, especially when car counts for a
specific automaker at a facility are high enough,”
said Jenkins. “I’ve seen technician productivity
increase by as much as 38 percent using OEM tools.”
He notes that factory tools more accurately
replicate the topology of the automaker’s vehicles’
electronic control modules (ECMs); include more
functionality since more calibration files, data
streams and algorithms are incorporated; and have
access to key coding and security system is usually
more complete.
“The desire of some shops to remain competitive and
stay current is another driver,” Jenkins added. “So
too are bad experiences with less capable tools,
especially when a facility has high car counts for
one or more automakers.” He explained that the
opportunity cost associated with sending a car that
one has in their shop elsewhere to be repaired is
significant. “Based on a 50/50 parts to labor mix
and a shop rate of $80 per hour, this translates to
$160 per hour lost revenue for shops.”
The lure of aftermarket scan tools
The initial cost of entry into buying and using
factory scan tools, as a percentage of gross profit
margin, can be huge, which in turn creates the
market for aftermarket scan tool makers. “But there
is confusion over what tool to buy, as well as the
compatibility between various aftermarket tools that
a shop uses,” Jenkins stated.
“In addition, many technicians are still
uncomfortable in a Windows/PC world, rather than
handheld scan tools, which many tool manufacturers
are moving toward.” The emergence of smart devices,
such as phones and tablets, just adds one more layer
of uncertainty to the purchase equation.
When juxtaposed against the much higher cost of
factory tooling, other concerns keep shops and
technicians from choosing OEM tools. For example,
there is the fear of obsolescence and having to
replace an already expensive factory tool or lose
the ability to repair some models. In addition the
cost of maintaining multiple OEM scan tools with
updates and service information and tool
subscriptions can be surprisingly high in some
cases, such as the case of BMW.
Jenkins also noted that in some cases, such as Ford,
functionality for a shop’s online Windows/PC tool
could just stop if a service information
subscription wasn’t renewed in time. In this event,
the aftermarket repair facility loses not only
access and capability to repair incoming models, but
also the same for older models that the shop was
already servicing. In addition, some automakers
charge an added fee when shops renew late.
Like being between a rock and a hard place, this
quandary leaves aftermarket facilities in a pinch.
Do they stay the course and do nothing? Do they
stick with aftermarket tools only? Do they
specialize in one, two or three vehicle lines with
factory tools? Do they contract out other lines or
problems their tools lack the functionality for (if
they even know that) to other shops or mobile
diagnostic specialists who have the factory tools to
perform tasks such as bidirectional controls,
complete ECM reflashes or deal with vehicle security
issues?
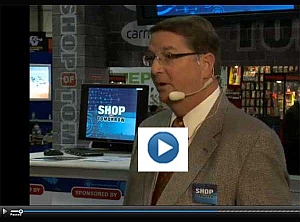
|
24/7 OBD II Telematics for the
Aftermarket
Carma Systems Inc.'s wireless OBD II
monitoring device is designed to be a
customer retention tool for aftermarket
service/repair facilities. It was first
demonstrated at AAPEX 2011, as part of the
iShop, the Automotive Aftermarket Industry
Association’s (AAIA) “Shop of Tomorrow”
initiative. Click on the image above and
watch the 15-minute video to learn more.
(Video — AAIA) |
Scan tool trends shaping the future of vehicle
serviceability
“For a single location independent aftermarket shop,
owning a high-quality, general purpose aftermarket
scan tool is a good first line of attack — it’s
quick, easy and dependable for most situations,”
Jenkins advised. “Next, the second type of scan tool
that this type of shop will need is a specialty
scanner that can fill the holes of the primary
general purpose tool. After that, once a facility
knows it has sufficient car counts, owning one or
more factory tools is a feasible option, followed by
purchasing a J2534 pass-through device.”
Using a mobile diagnostic super tech service is a
good option for smaller operations, Jenkins
suggested. “Typically, these businesses have
multiple OEM tools on-board their service vehicle
that are 3G/4G Internet-enabled. They also have more
ongoing experience with problems that may be a less
frequent occurrence for the shop, but more
commonplace for the mobile tech. These services
enable a fix that includes some profit for the shop,
is non-competitive in nature, avoids having to send
a customer or their vehicle elsewhere, and is
transparent to the customer as well.”
“I can see small groups of shops increasingly
evolving into pods of shops, ” said Jenkins. These
pods could pool resources and share costs, which
would allow the combined purchase of factory or
better quality aftermarket scan tools. “Within these
pods, tools could be designated a specific shop
location as their home base, then scheduled for use
by other shops within the pod, using courier
services or employees to mule tools between shops as
needed.
“Another arrangement that aftermarket shops might
use is what I call a hub-and-spokes pattern,”
Jenkins continued. In this scenario, multiple OEM
scan tools are kept at a central ‘hub’ location
manned by more highly skilled technicians. The hub
also advises the ‘spoke’ outlets about the viability
of repairs and other issues. If necessary, the spoke
shops will send more difficult work to the hub. “I
see the hub-and-spoke arrangement being used more
and more by multi-store businesses. It allows them
to better leverage their top technicians who have
the skill to use the full functionality available
from a tool.”
“The trend by scan tool manufacturers toward single
channel sourcing for all orders is also creating
problems for independent aftermarket service/repair
facilities,” Jenkins shared. The lack of competition
is slowing delivery and availability for some tools.
“Another growing issue is that while providing a
Web-based solution for tools delivery is easy, that
same Web-based solution is not so easy or effective
when it comes to scan tool repairs.
In addition, he demonstrated that the Web-based
delivery of scan tool information has led to some
automakers moving toward shutting down tools and/or
penalizing owners with high fees when subscriptions
expire before subscriptions are renewed.
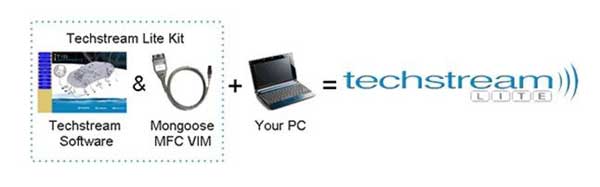 |
Improving Vehicle Service Readiness
Benefits Everyone
Toyota’s Techstream Lite is arguably the
closest to providing a “Holy Grail” solution
for the complete, yet affordable service and
repair of its brands — Toyota, Lexus and
Scion. The Web-based software solution
combines a Drew Mongoose J-2534 interface
device with access to factory scan tool and
complete service information via 2-day
subscriptions that enable dealer and
independent facilities to compete fairly —
saving consumers considerable expense when
compared to the costs associated with some
other automakers. (Image — Toyota Motor
Sales USA) |
Is there a scan tool Holy Grail?
“Many in the independent aftermarket fear getting
out-maneuvered,” Jenkins stated. “For example,
telematics services, such as General Motors’ On-Star
are viewed as a threat by some. Even some scan tool
manufacturers wonder if and how this kind of service
will affect them.” He said that it is important that
the aftermarket respond with a competitive
alternative. In addition, cloned OEM hardware and
software is becoming an issue for all parties.
“Whatever actions are taken to limit/stop cloning
will affect what the future of scan tool development
looks like.”
Jenkins noted that some still are looking for the
‘Holy Grail’ solution that brings together
everything a shop needs: a J-2534 common interface
for all OEMs, daily service information
subscriptions available for all automakers, one
smart scan tool device (e.g. tablet, phone) that can
handle all OEMs, cloud computing and more. The
hurdle? Shops don’t all agree on everything, nor do
all scan toolmakers, so expecting all automakers to
agree easily is unrealistic.
It may happen one day, or approach that, with the
adoption of open standards and common scan tool data
stream templates used by all scan tool
manufacturers. But it won’t happen any time soon,
nor will it occur if profits are given away. Just
think about what it would take to get Toyota, BMW
and Ford all on the same page here, let alone along
with all the scan toolmakers and the professionals
who service vehicles.
In the near term, Jenkins suggested, the independent
aftermarket can leverage the collaborative
relationships that certain organizations — such as
the Equipment and Tool Institute, the National
Automotive Service Task Force and the Society of
Automotive Engineers — have with automakers. The
goal should be to further the understanding that
moving the vehicle serviceability horizon from
end-of-warranty to the full lifetime of the vehicle,
wherever it is performed, is in everyone’s best
interests — consumers, automakers, tool and
equipment manufacturers and service/repair
professionals.
“No doubt, technological change will continue,”
Jenkins concluded. “What is certain is that the
wants, needs and desires of independent aftermarket
shop owners of scan tools haven’t changed over many
years. There is great opportunity for all who listen
and respond to aftermarket customer wishes.”
|
|