By Bob Chabot, Contributing
Editor
ETI Hosts NASTF General Meeting
Participation by ETI
members helps move NASTF forward
ETI hosted the National Automotive Service Task
Force (NASTF) Spring General Meeting, themed
“Improving Communication and Awareness” on May 2
during ToolTech 2011. The meeting consisted of a
business meeting and panel discussion, both of which
saw participation by ETI members. A full report of
the NASTF general meeting can be viewed at the NASTF
website, but a condensed recap of points and
business opportunities relevant to ETI members
follows.
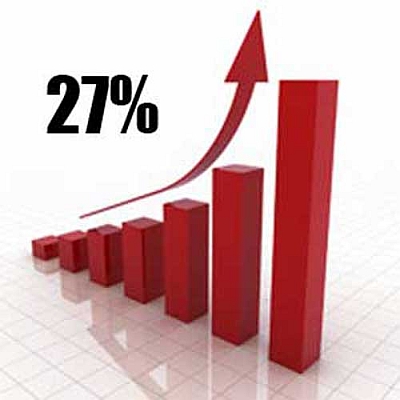
|
Growing
Awareness - NASTF sees partnering with
ETI to close service, tool and
training information gaps as a key
initiative to improving service/repair
professionals’ awareness of the
organization. (Image — NASTF) |
The meeting included a number of reports as well as
a panel discussion, moderated by Charlie Gorman, ETI
executive manager, which centered on helping
aftermarket shops improve service readiness by
improving industry-wide communication from OEMs
through to the aftermarket, employing common open
standards in tool design and manufacture and
adopting other key initiatives.
Here is a brief recap of the key insights that were
provided by the participants, a number of whom
represent current ETI members:
Theft-related vehicle service information and parts
are being securitized — Mary Hutchinson, NASTF
administrator, shared that automakers are beginning
to view NASTF’s Secure Data Release Model (SDRM) as
a viable means of providing vetted aftermarket
service/repair facilities with security- and
theft-related parts and service information, without
compromising original equipment manufacturer (OEM)
proprietary information or vehicle owner’s privacy.
Mercedes Benz USA has been piloting this in the
United States, and is now expanding the number of
parts available through the SDRM. Hutchinson also
shared that NASTF is working with the Canadian
service/repair market to enable the SDRM to be used
in the Canadian aftermarket.
The awareness of NASTF and its purpose is growing —
John Lypen of MOTOR Information Systems (an ETI
member), and the publisher and editor of MOTOR
Magazine, presented the results of a survey that
showed that 27 percent of aftermarket service/repair
shops surveyed were aware of NASTF and its purpose.
While pleased with the awareness level, NASTF board
members want to grow awareness to higher levels
across all industry segments.
Heavy-duty vehicle business opportunities exist —
Carl Kirk, the American Trucking Association vice
president for maintenance, information technology
and logistics, discussed the potential for industry
collaboration that could help the heavy-duty
industry meet mandated emissions regulations that
begin in model year 2013. He cited access service
information as well as improved tools and equipment
as two needs of the heavy-duty vehicle segment.
ETI and NASTF are building a meaningful scan tool
database and working to close tool information gaps
— Greg Potter, of DG Technologies (an ETI member),
serves as co-chair of the NASTF Tool and Equipment
Committee. He reported that this Committee is
nearing completion of an OE Tool Matrix that would
enable service/repair professionals, before they
purchase a tool, to compare feature sets of
available tools in the matrix to their needs. The
Committee is also liaising with ETI on two
initiatives — (1) Using ETI as a pathway to closing
OEM tool, service and training information gaps; and
(2) Encouraging tool and equipment makers to use the
NASTF Service Information Request (SIR) process to
document, identify and resolve these gaps.
Improving communication takes genuine and active
collaboration — “Collaboration can benefit OEMs,
Tier 1 suppliers, and the independent aftermarket in
a number of ways,” explained Shuvo Bahattacharjee of
Bosch ETAS, a business unit of Robert Bosch LLC (an
ETI member). “For example, standardizing a format
for data exchange for tool manufacturers could help
simplify vehicle diagnoses, enable key OEM
intellectual property to be protected, improve the
exchange of vehicle failure data over longer cycles,
foster the development of new methods for
prognostics and predictive diagnostics and reduce
legislative-driven requirements — all of which would
vastly improve the customer's brand experience.”
Improved communication and common open standards
could help reduce diagnostic tester development
costs — “There's lots of parametric data, in many
various forms, across many vehicle makes and models,
that requires a high effort to effectively manage,”
stated Bernie Carr, of Bosch Diagnostics, another
Robert Bosch LLC business unit. “Administering this
data creates a huge cost challenge for businesses.”
Carr also shared that aftermarket toolmakers want to
partner with OEMs. "If OEM and tool companies could
create and utilize a ‘Generic Data Template (GDT)’
for tool data, OEMs could output their data in the
GDT format that any toolmakers could then extract
then optimize for their customers.” He also agreed
that this kind of collaboration could lead to
“smart” tablets or other devices serving as
platforms for service information and diagnostic
tools for future service and repair professionals.
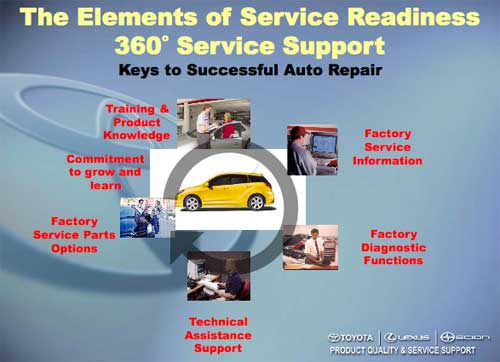
|
Service
Readiness is in Everyone's Interest
The shops and technicians that will
thrive in the future will invest in
"job-appropriate" service/repair
resources to be fully service ready at
an affordable cost. (Image - Toyota
Motors USA Inc.) |
Improved communication and common standards can
elevate service readiness — "Service readiness is
the act of having received the accurate service
training, service information, service tools and
service parts necessary to perform any diagnosis,
repair and/or adjustment that might be required to
support a product, in advance of product arrival for
maintenance, diagnosis or repair,” noted Mark
Saxonberg of Toyota Motor Sales USA. He then
demonstrated how improving communication; employing
open standard J2534-based diagnostics; providing
web-based service information via low-cost,
short-term subscriptions; and more meaningful
collaboration from automakers with Tier 1 suppliers,
tool and equipment manufacturers could vastly
improve service readiness for all dealer and
independent technicians. In the end, he concluded,
consumer brand experience is maximized, which
benefits everyone, from those who build cars through
to those who fix them.
The next NASTF general meeting will be held on Oct.
4, 2011 in Orlando, Fla., during Automotive Service
and Repair Week (ASRW).
|
|