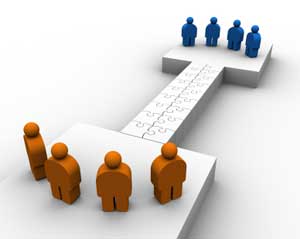
By Bob Chabot, Contributing Editor
Common Ground
Summer Tech Week is
authentic collaboration you can build new
business around
Sometimes you just have to be there. This is
especially so when to be able attend an automotive
industry event, you are required to sign a
nondisclosure agreement regarding the proprietary
data and information that is going to be shared.
Such is the case with such as 2011 Summer Tech Week
(STW), one of three core events that the Equipment
and Tool Institute (ETI) hosts throughout the
calendar year.
As a first time STW attendee, I had no grounded
concept of what to expect. But when all was said and
done, I was blown away by the depth and diversity of
what I had learned. I just can’t tell anybody about
it. Yet.
STW is unique in offering ETI members the
opportunity to dialogue with the Detroit- and
European-based automakers. It is the only industry
event where the each original equipment manufacturer
(OEM) involved provides attendees with the necessary
information, data streams and algorithms regarding
their inbound new model year vehicles as well as
updates for previous model years. By showcasing new
vehicles and associated technologies, the industry
can then discuss and develop the needed tools,
equipment and service/repair procedures that these
new vehicles may require.
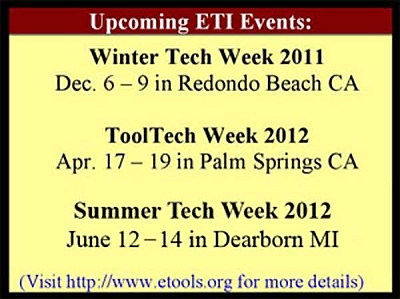
|
Your
attendance at ETI’s three core events—
ToolTech, Summer Tech Week and Winter
Tech Week — helps you maintain your
customer’s level of vehicle service
competency. Be sure to tell them why. |
The other two upcoming annual events hosted by ETI
are 2011 Winter Tech Week (WTW) and 2012 ToolTech.
Whereas WTW focuses on providing the same experience
for attendees as STW, but from the Asian automakers’
perspective, ToolTech is typically themed around a
broad industry concern, but is also chock-full of
networking opportunities, including unique
one-on-one private meetings between tool and
equipment manufacturers, distributors, OEMs and
other national accounts..
Attendees at STW can choose from several information
paths, which include the scan tool, under hood,
under car and collision repair groups, around which
each automaker tailors presentations. As a newbie, I
chose to attend a mix of the sessions for the four
groups and was welcomed warmly by whatever party I
lingered with. In addition to the different tracks,
each group held its own ETI vertical group meeting
during STW.
There’s so much I could tell you, but I am not
allowed to do that. In one sense, that makes writing
this article difficult. But in another way, the
nondisclosure tenet frees me to do something that
may well bring you, as a reader, more value, namely:
- Share my impressions and observations as a
first time attendee at STW.
- Summarize interesting conversations
surrounding the confidential presentations.
- Highlight several sales opportunities worthy
of your consideration.
- And just maybe, give you reason or cause to
attend STW or other ETI events.
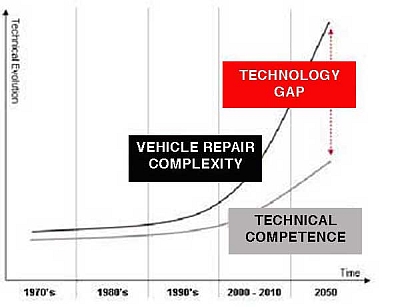
|
Attending
Summer Tech Week and other ETI core
events closes many service, tool and
training gaps before the rest of the
aftermarket even knows they existed.
|
ETI achieves what other leading
organizations do not
ETI doesn’t just talk and promote collaboration
between OEMs and the aftermarket. It breathes, acts
and delivers it. Please understand that I don’t make
this observation lightly. You see, I regularly
attend gatherings of the Society of Automotive
Engineers and am actively involved with the National
Automotive Service Task Force — both organizations
that foster and make the industry better via
collaboration.
But ETI — through events like STW, WTW and ToolTech
— distinguishes itself in ensuring that so much new
tool, equipment, service and repair knowledge is
willingly shared, discussed and disseminated, so
that the aftermarket is ready in time. In addition,
the level of respect between the OEMs and ETI’s tool
and equipment membership is ever-present; it is
strong enough that one can feel and savor it.
Let me put this another way: ETI closes many
service, tool and training gaps before the rest of
the aftermarket even knows they exist. Moreover, ETI
trail-blazes the path for SAE, NASTF and aftermarket
trade associations. Its members eyeball, touch and
begin preparing long before other organizations even
see these new vehicles. Granted, this is my
impression as a first-timer attendee, but it has
stayed with me since the event.
For instance, several OEMs at STW who have, or are
launching, all-electric vehicles indicated that they
are currently leaning towards wholesale replacement
of high-voltage components rather than the
replacement and repair of the separate parts that
comprise those components. The OEMs also shared that
wholesale component replacement would likely evolve
to larger sections of components being replaceable,
rather than entire units. Eventually, this will
morph to the replacement and repair of individual
parts of those components.
Knowing this, and the timing of change is critical
for everyone downstream of the OEMs. It not only
impacts tool and equipment development, but also the
timing of equipment and tools purchases by repair
facilities and even the nature of related training
for service professionals. In addition, regular
attendance at core ETI events will apprise the
industry should the pace of change quicken or move
in a new direction.
So what does this mean for you as an ETI member? Two
things — the first indirect, the other direct. I
write extensively for many of your aftermarket
customers, both on the mechanical service side and
the collision repair side. I can assure you that
this impression will be shared with those who grace
my words with their eyes. More directly, I feel
compelled to make a case for ETI members when it
comes to service and repair professionals
considering tool and equipment purchase decisions
from aftermarket manufacturers.
Being an ETI member has currency; it helps service
and repair professionals maintain competency. If I
owned an automotive service or repair facility, or
was a technician making a difference within one, I
would want and need tools and equipment that are
based on the latest and most accurate information
available. Anything less would be a disservice to
vehicle owners. My recommendation to professionals
will be to check and ensure that their tool and
equipment suppliers attend ETI events. If they
don’t, why do business with them? It’s more than
sorting wheat from chaff; it’s a matter of dollars
and sense.
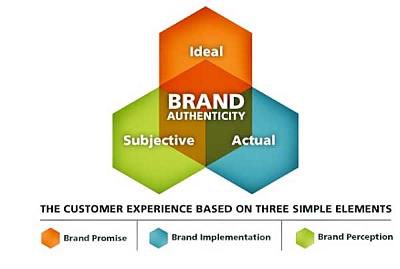
|
To
be truly authentic, we as an industry
must strive to enable and deliver
service and repairs that restore a
vehicle to its condition before a
tool, piece of equipment or
replacement part ever touched it. Are
we measuring up? |
Authenticity should be our entire industry’s
mantra
“Authenticity” was a word that popped up a few times
in conversations during breaks at two different
automaker presentations to the collision group.
These conversations centered on OE versus
aftermarket parts and on providing complete, “fully”
safe repairs.
One spontaneous conversation occurred at the end of
a session that included all ETI subgroups, just
before we broke out for separate presentations. A
few of us began sharing experiences centered on a
current collision repair practice that stipulates
the use of some salvage or or otherwise substandard
(certainly untested, let alone uncertified)
replacement parts, a practice often driven by
cost-driven insurance companies or sadly,
unscrupulous collision repair facilities. As I
listened, I felt like this group was talking to me —
for I am a member of the car-buying public.
While understanding the reasons to keep collision
repair costs down, the group basically reached the
consensus that consumers buy a vehicle that has
certain known safety ratings. Should that vehicle be
damaged in an accident, a consumer has reasonable
expectations that the vehicle to be returned to its
original safety ratings. When it comes to assuring a
complete, fully safe repair, our industry is quick
to push for proper collision repair techniques (e.g.
how to weld ultra high strength steels), yet somehow
we tolerate and are collectively mute about using
salvage or weaker (cheaper) parts for repair, rather
than either the OE parts that earned the safety
ratings or their aftermarket equivalents.
As a group sharing thoughts, we wondered why does
authenticity apply to all repair techniques, but not
to all parts used for a repair? Moreover, are we
truly serving the public with practices that allow
this? This dialogue left an impression left on me:
As a consumer, I want authenticity; as an industry
member, I am ashamed that we don’t always deliver
it. The chasm between is opportunity knocking.
That evening, a group of nearly 10 of us resumed the
discussion about OE versus aftermarket replacement
parts that had begun earlier in the day, but
expanded it to include both collision and mechanical
repair. We agreed that the time, money and effort
expended by the OE and aftermarket protagonists
ultimately obscured and prevented an authentic
solution be reached.
In our collective view, the authentic solution would
be to develop valid standards and independent
third-party testing to ensure that all replacement
parts offered for sale — whether OE or aftermarket
in its origin — meet those minimum standards, from a
safety and automaker warranty perspective.
Afterwards, several folks informed me that this
discussion and resolution would not likely have
occurred at any other venue than an ETI event.
Therein is another lesson from STW: The germ of a
solution is easily planted and can grow when we all
share — without agenda to serve, separate corporate
cultures to entrench or castles and moats to guard.
I can buy that.

|
Scan
tools are like icebergs. Much of the
automotive industry has no real
understanding of the depth or
complexity of the data required to
build the tools we use and often take
for granted. |
Just the tip of the iceberg
I thought I knew a fair bit about scan tools, at
least in my world. But with each ETI event that I
attend, I have breathed humility and seen my
ignorance. While I had heard about scan tool
information files, what I knew of them was rather
vague and nebulous. At STW, my eyes were opened to a
whole new dimension.
“There are three layers or categories of information
that scan tool manufacturers need in order to
develop their software,” ETI Executive Manager
Charlie Gorman shared with me. Just as an iceberg
isn’t visible to the casual observer and widens with
depth, when looking at a file of scan tool
information, Gorman noted that each of the three
successive layers in the hierarchy below is more
detailed and complex. He also explained that data
provided by OEMs at meetings like STW is then stored
by ETI in its TEK-NET library, where it is made
available to members.
These information layers include:
- Protocol documents — A detailed description
that describes an OEM's communications protocol
and how it differs from or a varies from ISO or
SAE specifications.
- Code and Parametric Data — Detailed
information that comes from Access databases or
Excel spreadsheets, or similar source documents.
- Functional Tests — These tests can be either
on-board (controlled by ECU) or off-board
(controlled by scan tool) in nature. They
include routines as simple as actuator tests to
those more complicated, such as cylinder balance
of brake bleeding routines.
“Of course, there are other things that ETI asks the
OEMs for, but these three categories are the heart
of the information,” Gorman continues. “Examples of
this extra information include vehicle
identification number (VIN) charts, network
architecture charts, J1962 connector pin-outs and
more. It is important to understand that there can
be several separate networks on any given vehicle,
so we need to know what modules are on what bus and
whether or not diagnostics are available for that
module.”
In simple terms, this increasing scale of scan tool
information complexity is like blowing up a map when
necessary by those who need to know more. The
overview shared by Gorman and the information
provided during scan tool group sessions at STW
provided me with a much deeper appreciation of the
complexities that tool and equipment makers deal
with every day. Many in my world, who use your
tools, take this detail granted or aren’t even aware
of it and the pitfalls that can be present. That’s
worth sharing, as is dealing with tool and equipment
manufacturers who are actively working with
automakers to improve vehicle serviceability.
While networking after a scan tool group session
with an OEM, I sat down with three scan tool
manufacturing company principals. I will not
identify here, but will share some of their
insights.
“Content is king,” one of them asserted. “It’s all
about getting the information at sessions like
today’s and putting as much of that new
functionality into scan tools as possible while
meeting certain market pricing points. The value of
an event like STW is that we get to know what we
need to know early and also ask about what we know
we don’t know.”
The conversation then evolved into what type of scan
tools aftermarket users preferred — handheld or
PC-based. For me it was interesting to watch these
competitors banter the pros and cons of each —
largely based on what form their own scan tools
took. But here’s what intrigued me: Each principal
acknowledged that the type of tool platform didn’t
really matter, content and functionality did. And if
anything, the only relevant driver for the type of
scan tool platform should be what the end-users —
technicians — wanted.
Given recent technological breakthroughs, such as
cloud computing, tablets, etc., I then ventured to
ask them about the possibility of automotive
technicians one day being able to own just one
“smart” device as a scan tool platform that was
capable of receiving and implementing scan tool
functionality delivered wirelessly as an app from
any or all aftermarket scan tool companies and/or
automakers.
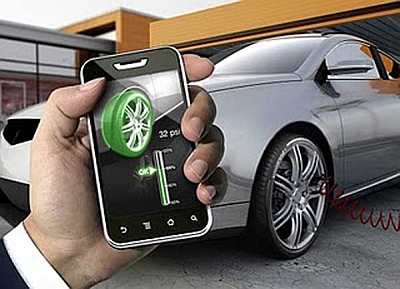
|
What
if all tool information and
functionality could be delivered to
any technician’s “smart” platform,
similarly to how service information
is today? That paradigm shift may well
be opportunity-in-waiting. |
Certainly that would take common standards and a
generic data template as Bernie Carr of Bosch
Diagnostics had suggested recently at ToolTech 2011.
But just imagine a future scenario wherein current
scan tool manufacturing evolved into tool
information providers who (like vehicle service
information providers today) delivered their scan
tool functionality to one device that would
interface with a vehicle. Competitive edge would be
rooted in the richness and accuracy of content, the
ease of common navigation and use across brands by
technicians and other user-beneficial factors that
make a vehicles more serviceable and technicians
more productive.
Here’s the rub: ETI’s Summer Tech Week is part of
the cure that our industry needs. I suspect that I
am pretty typical of those technician and shop
customers that you all deal with. We use tools and
equipment that you build. Yet together, you, the
OEMs and service/repair professionals collaborate to
enable the improved servicing of vehicles that the
public buys. That ongoing dialogue is allowing us to
build a common perspective that helps us all become
more efficient and effective. That is a win-win
scenario for everyone.
|
|