
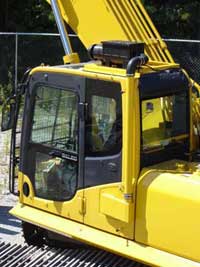
|
Contributed
by
Bob
Chabot
The Future of Heavy-Duty Cab Environments
Will future
environmental
cabs be government-regulated or free market-driven?
Cleaning up heavy-duty, off-road operator enclosed cab environments is
an ongoing struggle. Medical research shows extended exposure to a wide
variety of airborne particulates can be harmful to operators. Industry
experience also tells us that extended exposure to a wide variety of
airborne particulates is harmful to equipment. Both have consequences
that can be measured in dollars and lives.
Without consultation, government regulation can
lead to
dead ends
|
The business of
removing dirt from the air prior to its entry into an intake on an
engine or the HVAC system knows no geographic boundaries. Airborne
particulate — whether at a coal mining operation in Alabama, a
sandstone quarry in Australia or inside a waste recycling facility in
Europe— has a devastating effect on heat exchangers, evaporator cores,
electronic equipment and the environment inside an operator cab.
As industrial engineers grapple with finding cost-effective and safe
solutions, governments have mandated and are considering more
regulations and specifications for cleaning up cab environments. For
example, the U.S. Occupational Safety & Health Administration
(OSHA), has developed industry-specific, maximum exposure level
measures for most airborne toxins, gases and particulates. Regulations
typically focus on PELs during a work shift as the primary guideline.
In the past, the health effects of hazardous working environments were
considered part of the job. Today, keeping workers healthy has
governments, labor unions and insurance companies pushing to reduce
workplace exposure to breathable dust and airborne toxins commonly
associated with operating heavy duty equipment. These measures include
Occupational Exposure Limits (OEL), Permissible Exposure Limits (PEL)
and Time Weighted Average Exposure Limits (TWA).
Under the guise of ‘public safety,’ regulators have sometimes moved
ahead of, and often independently from, research scientists and cab
manufacturers when mandating air quality standards that were not
achievable with known technologies. This lack of consultation can lead
to misallocated capital, increased machine cost, a frustrated
engineering community and consequences worse than the original concern.
|
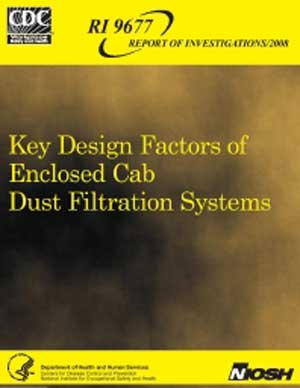
Setting
the Bar
The
Centers
for
Disease
Control
published Key Design Factors of Enclosed
Cab Dust Filtration Systems in 2008, which has become the seminal work
in understanding the fundamental requirements of heavy duty cab and
HVAC design. It demonstrated that high-efficiency filtration and zero
seal leakage are required to provide high-quality air environment to
the HVAC and cab operators. To read the complete study, click
here. (Images — Centers for Disease Control)
|
Measuring
‘In-Use’ Heavy Duty Emissions Data
The Portable
Eemissions Measurement (PEM) unit — developed by the EPA,
Sensors Inc. and Eastern Research Group — can be temporarily fitted by
crane to heavy duty equipment to measure CO2, CO, THC and NOx emissions
while the equipment is in use. (Image — Sensors Inc.)
|
“Sometimes, in
trying to solve a relatively harmless problem we create
a far more dangerous one,” notes Jeffrey L. Moredock, vice president of
sales for Sy-Klone International <
Link
—http://www.sy-klone.com>
. He cites a U.S. regulation that required that diesel engine exhaust
be reburned to reduce the black smoke or unburned diesel fuel
emissions. Reburning the exhaust caused subsequent emissions to go from
relatively large particle to much smaller particles in the 0.3 micron
size range. The human respiratory system cannot clear itself of these
smaller particles, which remain in the lungs and are more likely to
cause illness.
In addition, the accurate and practical measurement of cab air quality
with sensitive testing instruments is challenged by real-world
humidity, high dust concentrations and intense vibration. In 2009, for
example, the European Union approved a regulation that required so high
a degree of accuracy in the measurement of the contaminants in
agricultural sprayer cabs that even the most sophisticated labs in the
world would have a difficulty measuring. Any original equipment
manufacturer (OEM) shipping to Europe was faced with an expensive,
impractical, unfeasible task.
|
Recently, the Society of Automotive
Engineers <Link
to
article
—
http://www.sae.org/mags/SOHE/9258
> reported the EPA and its
research partners have developed a portable emissions measurement unit
that can be temporarily fitted by crane to heavy duty equipment. The
EPA says that in a small field project, it was able to determine, while
in-use, time-resolved (1-hz) gaseous pollutant mass emission rates
(CO2, CO, THC and NOx) of heavy duty equipment. It remains to be seen
if this device can maintain its efficacy amidst humidity, dust and
vibrations over time.
|
Cleaner
Air
Plus
Cost
Reduction
T A Hall General
Contractors Inc. operates a coal operation in Alabama. Their machines
run continuously and experienced regular premature HVAC failure – on
average every three months – due to coal dust clogging the evaporator
core. The average repair cost per incident exceeded $7,000. After
installing Sy-Klone’s International’s RESPA® Cab Air Quality System
equipped with Gideon® particle separation technology, the new
machine experienced no HVAC failure in the following six months of
operation and there was a dramatic reduction in filter replacement. The
above images show the evaporator core before (left) and six months
after (right) operating with the new technology (right). (Image —
Sy-Klone International) |
Those closest to the problem are in the
best position to solve it
Modern environmental cabs and associated HVAC systems must increase
operator productivity, reduce breathable particulate and work
maintenance-free for longer periods of time. In the absence of
industry-provided solutions, it’s true that regulators will mandate
change ‘in the public interest,’ without regard or concern for the
impact on cost or productivity. Consequently, industry cannot wait for
the government to regulate them before taking action.
In addition, as exposure measures become more stringent, complying
becomes difficult. “If industry waits for the regulators to dictate cab
design, they will find themselves bound by a spool of red tape that
creates huge disincentives to innovation and ultimately creates a
dependency that is unsustainable for the heavy equipment industry, its
customers and its operators. Recognizing that health and safety also
affect the company’s bottom line, OEMs must look for ways to reduce
workplace exposure to breathable dust and airborne toxins,” says
Moredock.
“Industry is in the best position to make cost -effective,
consumer-driven improvements to their operator cabs which enhance the
value of the machine and the marketability of their product,” he adds.
“When regulators dictate solutions, they are often difficult to
implement, costly to administer and ineffective in addressing the
problems.”
|
Moredock shares an example where
collaboration worked. “Recently, the
Sy-Klone representative in Canada was following up with the
Occupational Safety and Health Administration regarding their interest
in our environmental cab solution — RESPA® with Gideon®
particle
separation technology — which we had demonstrated at a local trade
show.”
“Curiosity regarding our product resulted in an invitation to
demonstrate it to the OSHA staff. They also told us, ‘We are going to
let industry figure out the best solution. However, we want to
understand your RESPA® system, and we would appreciate your
willingness
to share it with our staff.’ This was a great response from a
governmental agency and will be one reason, I believe, that Canada will
be successful in getting real solutions into the market place.” |
A fork in the road ahead
“The question is simple,” Moredock asserts. “Will industry act in the
consumer’s best interest and provide the most cost-effective solutions,
or will government regulation be the driving force for change? The best
approach puts industry in the driver’s seat, as it results in lower
costs, higher performance environmental cabs and ongoing technological
advancement.”
Beyond operator safety, there are other compelling economic reasons for
improving the air quality in an enclosed cab environment. The challenge
of employing high-efficiency filtration to keep dirt off the evaporator
core and out of the operator environment over extended periods of time
allows the rethinking of HVAC and environmental cab design.
Conventional engineering effort has been focused on how to keep the
HVAC system working properly while pressurizing the cab. The most
common approach to cleaning air before it goes into the fresh air
plenum is with a fresh air filter. But with very little loading, these
filters become too restrictive for the fan to effectively pull air
through it without stalling. To prevent this, a blower motor was then
employed to draw more fresh air through the fresh air filter. Yet this
also pulls 100 percent of the dirt in the air stream onto the filter,
causing it to clog quickly and lose the ability to pressurize the cab.
The addition of a nonpowered precleaner decreases blower motor
efficiency, as it cannot overcome the restriction added by the
precleaner.
|
A Global Industry-Led
Solution
Sy-Klone
International’s patented RESPA® Cab Air Quality System, equipped
with powered Gideon® particle separation technology, allows mobile
enclosed cab HVAC systems to perform at cleanliness levels previously
impossible to attain required levels in many industries and
jurisdictions around the world. (Image — Sy-Klone)
|
This typical industry approach has been a
series of compounded band-aid
attempts to improve filtration that resulted in low filtration
efficiency, more frequent filter changes, filter seal leakage and
machine downtime. Moredock says that adequate technology to bring
environmental cabs into compliance exists and that the industry has the
technology and know-how to resolve issues before they become objects of
the regulators’ attention, anywhere in the world.
“The technology that allows for major advancements in cab air
performance is relatively new and unknown to many cab manufacturers,”
adds Moredock. “Nor is it is understood by many in the engineering
community. In part, this is because the engineering issues associated
with developing a functional environmental cab in a heavy debris
concentration, high-vibration work environment are complex.” |
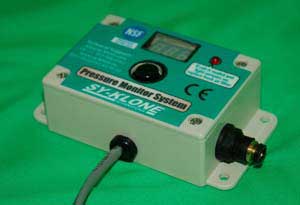
Monitoring
Protects Value
A pressure monitor and in-cab telemetry system proactively
monitor critical, real-time data within a HVAC system. This enables
cost-effective cab air filter changes and the identification of
potential failures
before they result in costly machine downtime. (Image — Sy-Klone)
|
An industry-led
solution for a multi-industry, multijurisdiction problem
OEMs sell their products to more than one country, each with its own
regulations that drive up costs further and decrease manufacturing
efficiencies. On one hand, the operator cab is one of the least
expensive environments in which to control air quality, making it a
major factor in reducing the average daily exposure rate to harmful
substances. On the other, the inability to provide high-efficiency
fresh and recirculated filtered air had been the greatest roadblock to
the development of sustainable, low-cost maintenance environmental cabs.
“But that has recently changed,” says Moredock. “The future of
environmental cabs will include sustainable, low-cost, powerful
engineering controls that will empower the operator and owner to
maximize the productivity of the machine by minimizing operator and
machine downtime. Sy-Klone International’s technology — the patented
RESPA® Cab Air Quality System with a powered Gideon® precleaner
— is one example of an industry-driven solution for clean, safe
enclosed cab HVAC systems.”
|
“RESPA® is the bridge to the future
of environmental cabs,” Moredock
explains. “It is able to cost-effectively provide high-efficiency fresh
and recirculation air filtration, long filter service life, cab
pressurization and extended service intervals on HVAC components. In
addition it provides high-quality air to the operator allowing for
compliance to the myriad of air quality regulations within various
industries and countries around the world.”
Moredock insists that by taking a proactive approach, environmental cab
technologies will continue to advance. “Industry can grow with less
regulatory burden, while also providing the customer with what they
want — low cost, low maintenance, environmental cabs that protect the
operator and increase productivity.”
Would you agree?
|
|
|